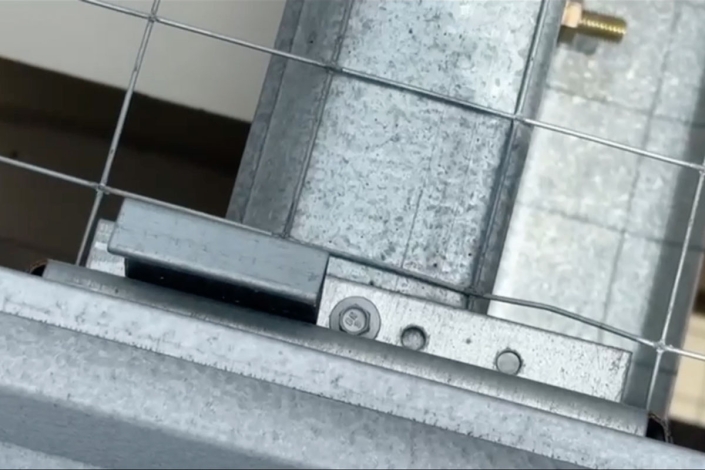
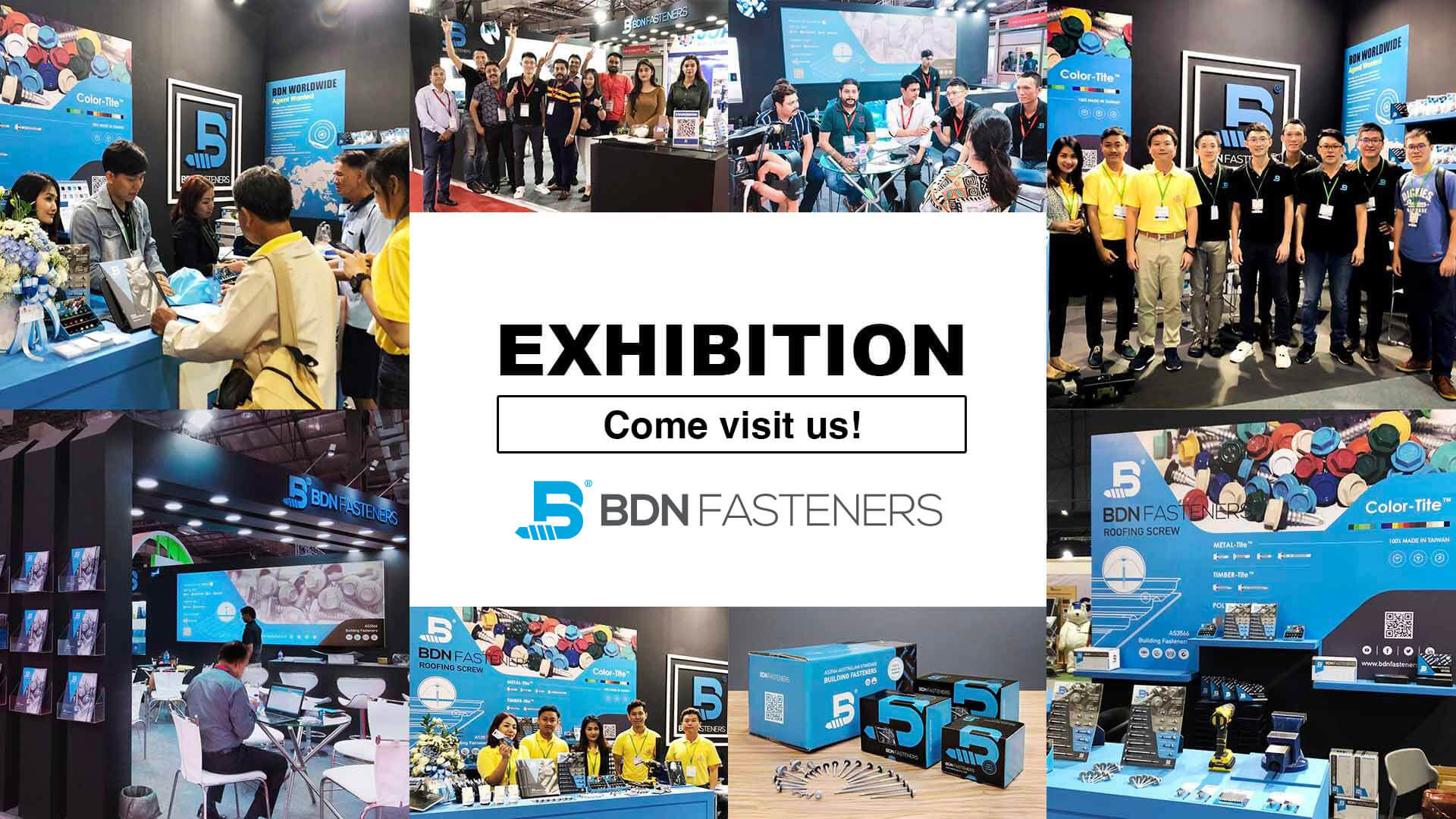
Check Out our Upcoming Exhibitions
Taiwan Hardware Show (14-16 Oct,2025)
|Exhibitions| See you there!!
Taiwan Hardware Show(THS) 2025
Date: 14-16 Oct, 2025
Location: Taichung International Exhibition Center
Welcome!
BDN Fasteners® Booth No.
International Hardware Fair Saudi Arabia (Jun 16-18, 2025)
|Exhibitions| See you there!!
International Hardware Fair Saudi Arabia 2025
Date: 16-18 Jun, 2025
Location: Riyadh International Convention & Exhibition Center (RICEC)
Welcome!
BDN Fasteners® Booth No. D41 (Hall 1)
ARCHITECT 2025 (30 Apr - 5 May, 2025)
|Exhibitions| See you there!!
ARCHITECT 2025
The ASEAN’s Largest Building Technology Exposition
Date: 29 Apr – 4 May, 2025
Location: IMPACT, BANGKOK
Welcome!
BDN Fasteners® Booth No: L200/1
Fastener Fair Global 2025 (25-27 Mar, 2025)
|Exhibitions| See you there!!
Fastener Fair Global 2025
Date: 25 – 27 March 2025
Location: Messe Stuttgart, Germany
Welcome!
BDN Fasteners® Booth No. 5-2812
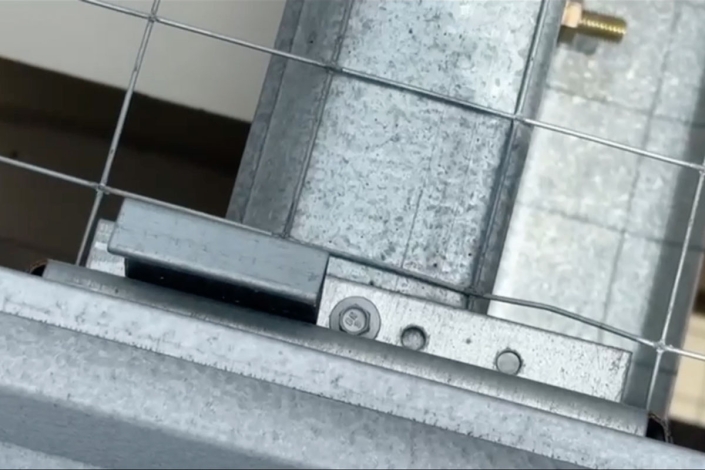
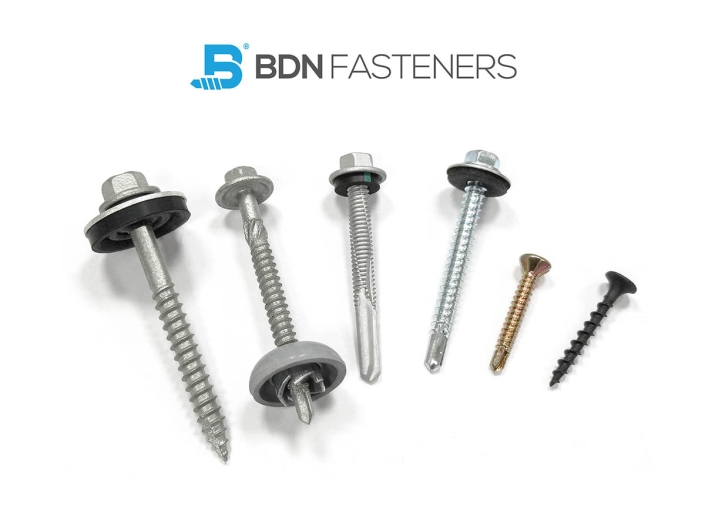
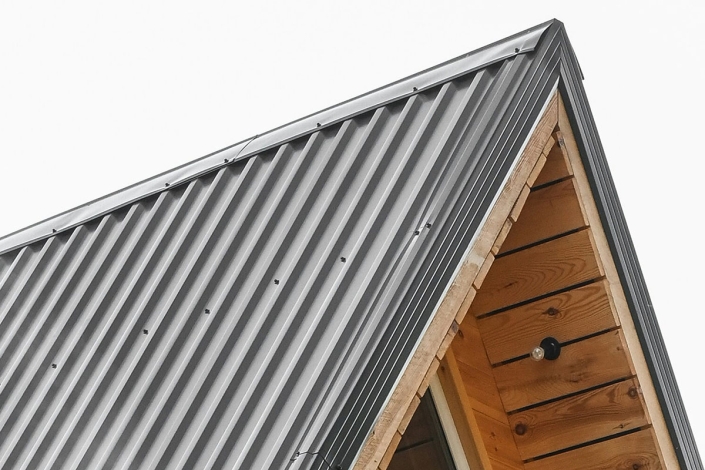
BDN Fasteners
BDN Fasteners (Broaden Worldwide Co., Ltd) is an ISO-9001 Certified Quality Supplier-Manufacturer of Australian Standard AS3566 self-drilling and self-tapping screws in various coatings for steel to steel and steel to timber applications. Our headquarters are in Taiwan and we operate sales and marketing offices in India and Thailand.
Founded in 2009.